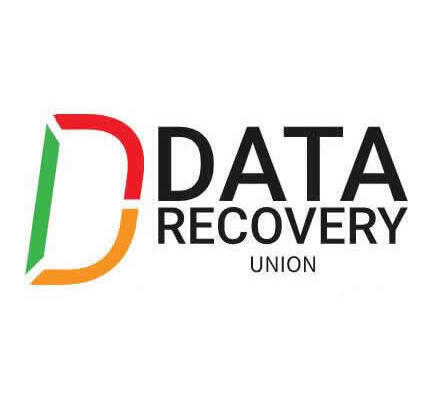
Hardware Life Cycle Management(Part I)
Every IT professional can tell a horror story about an upgrade, roll-out, or migration gone awry. So many factors are involved; hardware, software, compatibility, timing, data, procedures, security protocols, and of course the well-meaning but imperfect human.
Over 2008, IT departments and staff can look forward to a number of upgrade projects for their computer system infrastructure. According to Gartner, Inc., the number of PC shipments during fourth quarter 2007 increased 13.1% over the same period in 2006. Global PC shipments during 2007 increased 13.4% over 2006 – equating to 271.2 million units in 2007.
While a slower economy than in previous years may lower the number of units, the fact that organizations have been investing in new units shows that Hardware Life-cycle Managementis still a mainstay of corporate IT’s responsibilities and will continue to be such.
IT professionals realize that scheduled change is a pattern for the industry. Whether this change involves accommodating new users, replacing old servers, or upgrading staff to newer systems, there is always change within the computer organization. Sometimes it is easy to only rely on hardware or software budgets for your roadmap. However, these budgets may be short-sighted and lack proper planning. Using accounting budgets alone to manage hardware may not take into consideration the overall life span of the equipment.
Equipment/software life-cycles and your road map
Managing IT equipment and product life-cycles is an important function of IT department staff. As a goal, equipment life-cycle management should reduce failures and data-loss because computer equipment is replaced before it fails, and it should reduce the total cost of equipment management over its lifetime. Depending on the organization, equipment life-cycles are based on different criteria.
• Warranty expiration: If your IT infrastructure has a mix of equipment in place, with different makes and types of equipment, then your warranty-based product life-cycle management will be complicated. Using this approach is not only short-sighted, it also mirrors the first time you bought the equipment. Consider the expanding department who needs to plead with the CFO or budgetary manager for a non-planned equipment purchase. Three years later when the warranty expires, the department will be back again on their knees begging for replacements or an extension to the expiring warranties. Whichever the case, it will be an unplanned expense.
• Waiting until equipment fails: In our economy, budgets are tight and management rightfully wants to get the most production or usage out of a piece of equipment before having to replace it. This approach is very risky and will usually cost more in the end. IT equipment rarely fails at a “convenient” time. If you’re lucky, the failure occurs during a slower period and your IT department is equipped to get you back up and running quickly. In reality, this is not usually the case. Consider the real cost of equipment failure if it is month-end or year-end and the server with the financial data crashes; or a company has just secured a large contract and at the eleventh hour, one or more workstations fails or becomes intermittent causing wasted downtime on the project and inefficient use of personnel resources.
• Capital expense budgets: Some IT departments base their product life-cycles on departmental accounting policies for capital expense purchases. Of course, this alternative method can have a knock-on effect when there is a business need for expansion and this wasn’t considered in the fiscal budget. Additionally, in larger user environments, departments may have control of their own capital expense budgets, so there may be many departments with different budget needs. When the life-cycle of one department’s equipment is complete, the number of fragmented purchases may actually reduce your company’s buying power. In contrast, a more structured approach would concentrate equipment purchases to various times throughout the year. This method is preferred by CFO or budget managers who will use a predefined purchase allocation per business unit or department to facilitate budget planning for the next year.